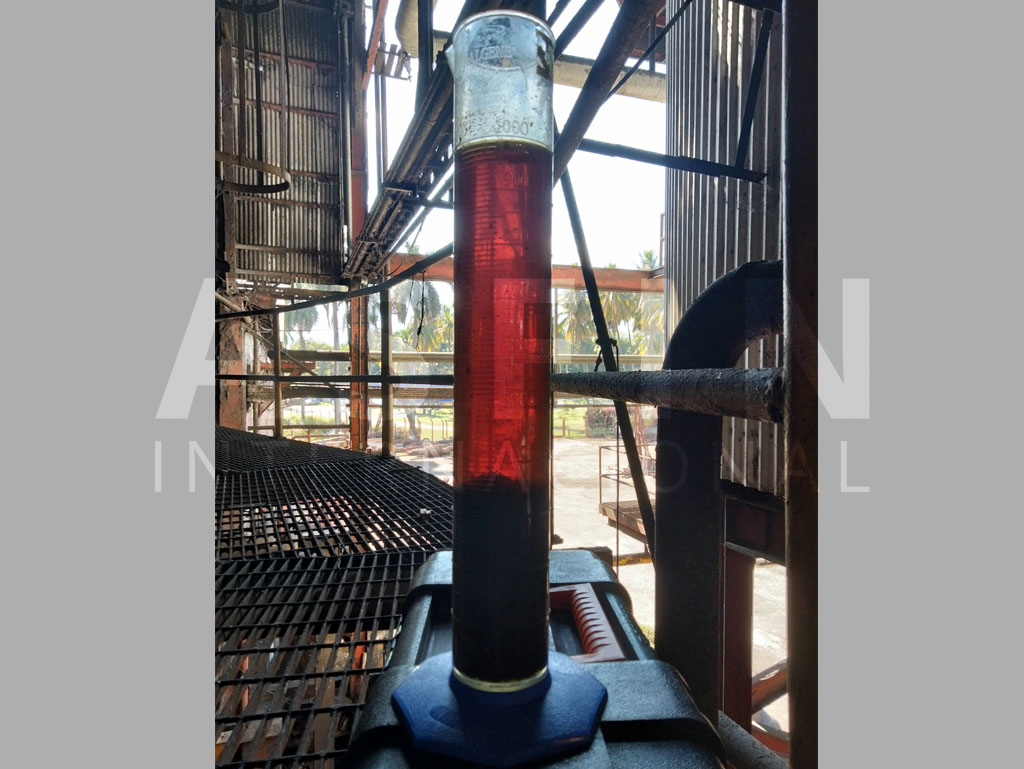
Juice Clarification Process
Problem
The sugar mill had problems in its juice clarification process, such as the presence of sludge in the clarified juice (overflow) and extraction of sludge (cachaza) with a high presence of juice (very little compaction). As a consequence, the plant had to reduce the cane milling rate and, in some cases, stop milling to allow time for an effective juice decanting.
It is important to note that each mill has its own operating conditions, due to the different types of sugarcane, soils and fertilizers applied.
The preparation of the 0.05% flocculant was observed to be correct. The pH and temperature of the alkalized and heated juice was within normal parameters.
The dosage of the polymer used was 11 ppm, which seemed to be a very high value.
Solution and Results
Initially, we proceeded to perform laboratory (or jar) tests with the super high molecular weight anionic ASFLOC™ flocculants to determine our best reagent in the clarification process.
In these in-plant tests with samples of alkalized and heated juice before the flash tank, we evaluated the settling velocity and the compaction of the produced sludge (cachaza), ASFLOC™ 037 VHM being our best reagent.
With the acceptance and support of the customer, industrial tests were carried out for 3 days achieving very satisfactory results at a dosage of 7 ppm. A totally clean clarified juice and a very well compacted sludge (cachaza) were obtained.
The customer approved the change of flocculant to ASFLOC™ 037 VHM and its continuous consumption.
Benefits
- Excellent juice clarification
- Better handling of compacted sludge (cachaza) for filtration and sucrose recovery.
- Continuity in the milling process and higher sugar production.
- 36.5% lower polymer consumption and therefore the same reduction in the number of preparations.
- Considerable cost savings