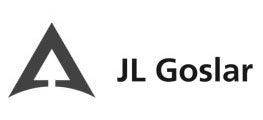
About us
JL Goslar is a leading manufacturer of equipment, components and semi-finished products, in lead and tin, for the chemical, metallurgical and nuclear industries.
Founded in 1906 in Goslar, in central Germany, it currently has 160 employees operating in two plants. Both personnel and machines have extraordinary capabilities in many lead applications and manufacturing processes, such as rolling, casting, extrusion, machining and, most importantly, homogeneous lead coating.
In the construction of equipment for the chemical and metallurgical industry, lead has a long history due to its extraordinary characteristics, such as:
• More severe corrosion resistance
• High density
• High conductivity
• High ductility
• Low melting point
• Low cost and easy maintenance
JL Goslar has been producing chemical and metallurgical equipment for more than 60 years. The commonly manufactured products are:
• Wet electrostatic precipitators for gas cleaning in sulfuric acid plants
• Star coolers for gas cooling in sulfuric acid plants
• Reactors lined with homogeneous lead and autoclaves for various applications in chemical and metallurgical plants
• Tanks and containers for the transport of bromine and other highly corrosive products
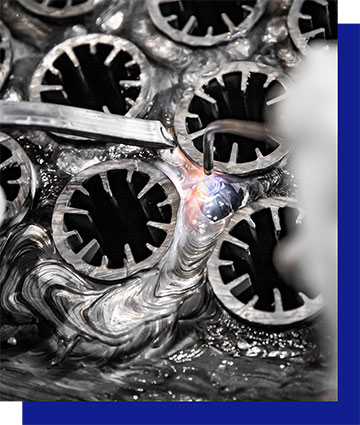
JL Goslar’s unmatched strength lies in its enormous capacity to provide all services, manufacture products and face the challenges, present and future, around lead and tin. The scope of the projects not only includes the manufacturing of parts or equipment, but also the design, engineering and development, including also the legal approval processes that are usually required for new products. In addition, we are usually responsible for their installation, subsequently ensuring continuous and efficient service, through inspections, updates, corrective actions and maintenance.
We offer
Since 1972 JL Goslar has manufactured Wet Electrostatic Precipitators (WESP) for gas cleaning. For five decades, we have produced, installed and renovated numerous precipitators around the world, with projects in Europe, Asia, Africa, Central America and South America.
In addition to having experience in the installation, repair and improvement of different designs of wet electrostatic precipitators, we are specialists in the manufacture of new electro-filters.
The quality of our complete lead-coated filter systems or their spare parts responds to our interest and commitment to details, and the excellent skill of our staff. Likewise, our qualified and experienced work teams provide the necessary precision to assemble the wet electrostatic precipitators perfectly aligned and leveled, guaranteeing the highest possible efficiency, always. Coupled with the enormous mechanical stability of the housing and its excellent resistance to corrosion, as well as the high quality of all its internal components, our electro-filters have been working successfully for decades.
Fields of application
• Non-ferrous metallurgy
• Sulfuric acid production
• Thermal power plants
• Chemical plants
• Coke production
References
• Nyrstar, Europe
• Venator, Europe
• Aurubis, Germany
• Boliden, Sweden
• Codelco, Chile
• Industrial Mining Mexico, Mexico
• Metalúrgica Met-Mex Peñoles, Mexico
Naturally, even the best equipment needs maintenance and help in emergencies. JL Goslar has extensive experience repairing wet electrostatic precipitators and overhauling and upgrading existing equipment. In emergency cases, we are your partner to find immediate corrective measures to minimize downtime.
Since equipment availability and reliability are crucial for every company, we recommend scheduling a periodic review of your precipitators. Our experts travel around the world to provide a detailed inspection of the condition of your equipment.
“Estrella” Coolers have been manufactured by JL Goslar for several decades. Its name responds to the fact that lead tubes have a star shape, or some other profile, which increases the surface area of the tube and, therefore, improves cooling efficiency. The material chosen for this equipment is fine copper lead, a reliable material with advantages such as impermeability to gases and liquids, and exceptional corrosion resistance against acids. Chillers used with seawater have a uniform or corrosion-resistant internal lead coating.
Scope
The first step in the production of a new Estrella Chiller is to convert your requirements and specifications into a custom design, considering the specific characteristics of your plant, the equipment and the composition of the gas.
Based on the design, the production process begins by precisely defining and analyzing the composition of lead in our own laboratories. The manufacturing of the steel body and the homogeneous lead coating are carried out in our state-of-the-art workshops, which guarantees efficient production in terms of cost and time. The tubes are manufactured in a continuous casting and extrusion press. This gives us enormous flexibility in terms of the length and profile of the tubes.
Likewise, the excellent quality of JL Goslar’s Star Coolers is guaranteed by continuous testing during the manufacturing process and subsequently a pressure test. Quality inspections adhere to JL Goslar’s own Special Quality Assurance Program.
If you would like to repair or modernize your plant, JL Goslar is the right partner to dismantle your existing chillers, recycling the internal parts in our foundry and reusing the lead in the manufacture of new parts.
Fields of application
• Non-ferrous metallurgy
• Sulfuric acid production
• Thermal power plants
• Chemical plants
References
• Nyrstar, Europe and the United States
• Asturiana de Zinc, Spain
• Aurubis, Germany
• Boliden, Sweden and Norway
Homogeneous lead coated anodes for pickling stainless steel and cold rolled steel.
Some other applications, are:
• Production of very thin sheets of pure copper
• Anodized
• Chrome and zinc plating
The advantages of using JL Goslar anodes are:
• As a result of decades of experience collaborating with users with different requirements, we not only manufacture, but we can also advise and suggest optimizations for your process.
• These anodes have a long service life due to their very high quality manufacturing.
• Manufacturing processes allow the production of a large quantity of anodes in a short period of time.
• The variety of anode sizes and shapes is almost limitless. We have been able to meet all the requirements of our customers.
• We process all possible combinations of materials that the client requires, such as lead and lead alloy with steel, copper or bronze, etc.
• Surfaces can be specially sandblasted or mechanically processed.
• We also apply collision protection to the anodes to protect them.
• The end result is that our clients get the most benefit-cost possible.
Among our clients for lead lined anodes are:
• ThyssenKrupp Nirosta, Germany
• Outokumpu Stainless AB, Sweden
• Outokumpu Stainless OY, Finland
• Outokumpu Special Strip, UK
• APERAM (ArcelorMittal), Belgium
• APERAM (ArcelorMittal), France
• APERAM (Acesita), Brazil
• POSCO, South Korea
• BAOXIN China
• Acciai Speciali Terni, Italy
• Marcegaglia, Italy
In addition to working with engineering companies such as:
• SMS SIEMAG, Germany
• Andritz, Austria
• Danieli, Italy